NDT là gì? Tìm hiểu về Kiểm tra Không Phá Hủy trong Công nghiệp
Tìm hiểu 12 phương pháp kiểm tra không phá hủy (NDT) giúp đánh giá chất lượng vật liệu, thiết bị công nghiệp mà không gây hư hại hay gián đoạn.
NDT
Admin
14 phút đọc
Kiểm tra không phá hủy (tiếng Anh: Non-Destructive Testing – viết tắt là NDT) là phương pháp đánh giá, kiểm tra tình trạng và chất lượng của vật liệu, linh kiện hoặc kết cấu mà không làm hỏng, không gây biến dạng hay phá hủy mẫu thử.
NDT thường được sử dụng như một thuật ngữ chung để chỉ các phương pháp kiểm tra không phá hủy, công cụ kiểm tra, hoặc thậm chí toàn bộ lĩnh vực kiểm tra không phá hủy.
Mục đích NDT
Giúp phát hiện sớm các khuyết tật như nứt, rỗ, hàn lỗi hay ăn mòn để đảm bảo an toàn trong vận hành và kéo dài tuổi thọ thiết bị. Ngoài ra, NDT còn giúp kiểm soát chất lượng sản phẩm trong quá trình sản xuất, hỗ trợ công tác bảo trì định kỳ, và đáp ứng các tiêu chuẩn kỹ thuật khắt khe trong nhiều ngành công nghiệp như dầu khí, hàng không, xây dựng và năng lượng. Đây là một công cụ quan trọng giúp doanh nghiệp giảm thiểu rủi ro, tối ưu chi phí và nâng cao độ tin cậy của hệ thống.
NHỮNG PHƯƠNG PHÁP KIỂM TRA KHÔNG PHÁ HỦY PHỔ BIẾN
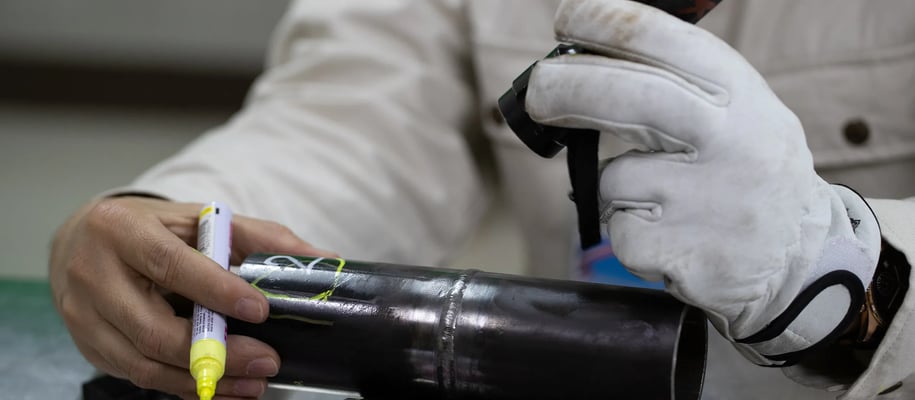
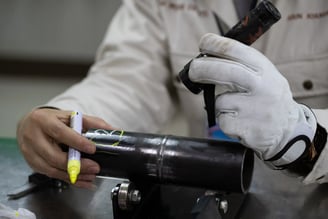
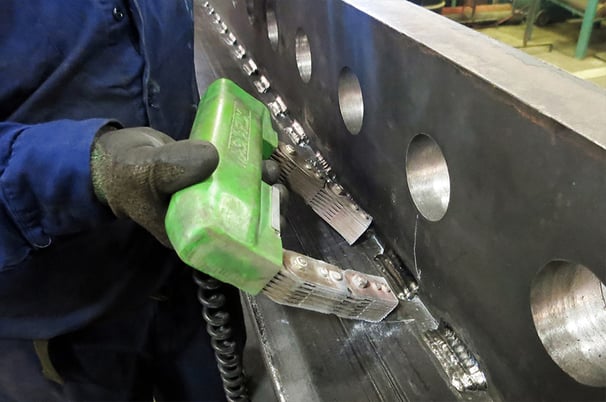
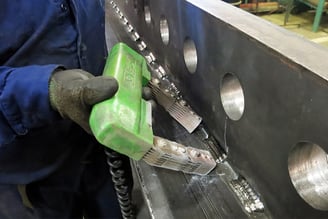
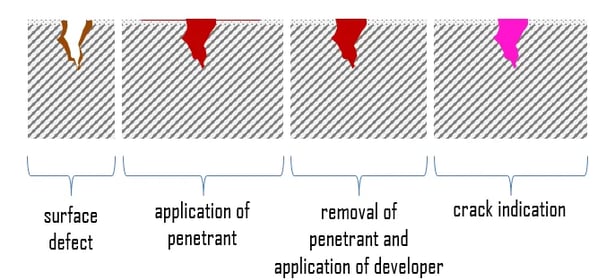
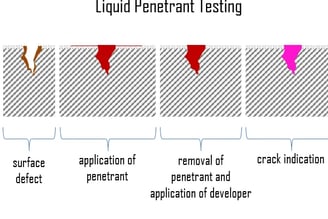
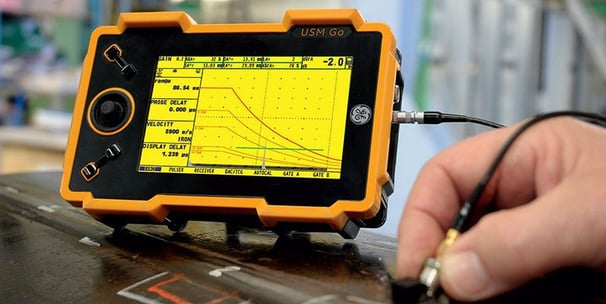
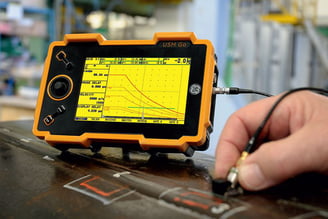
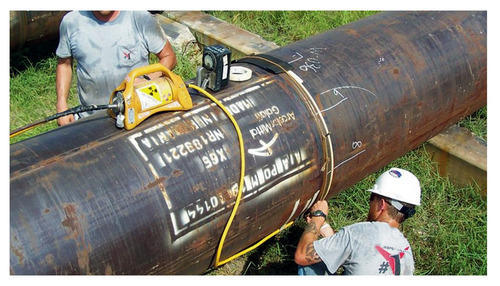
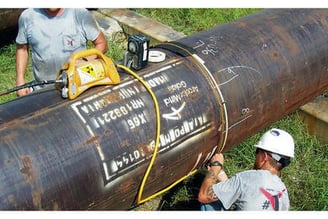
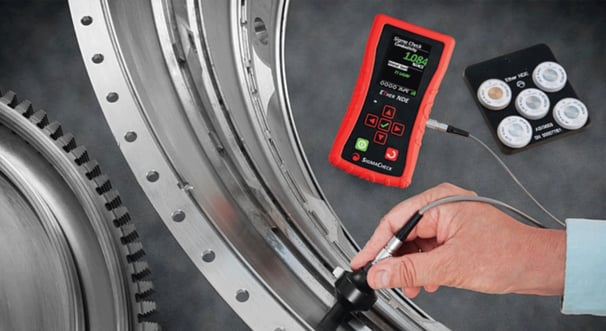
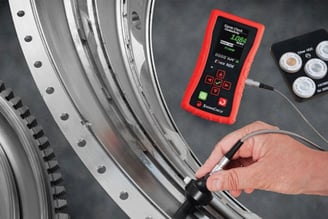
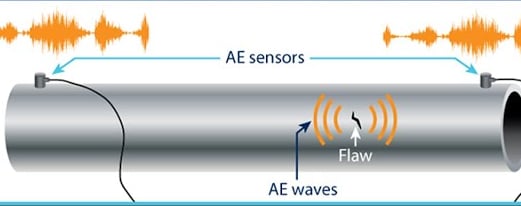
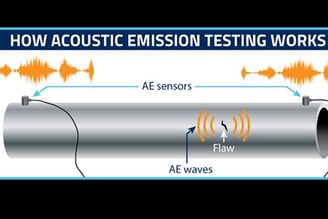
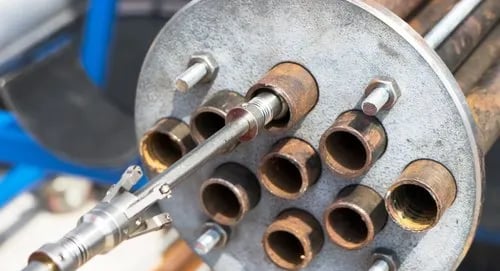
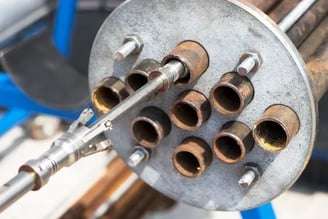
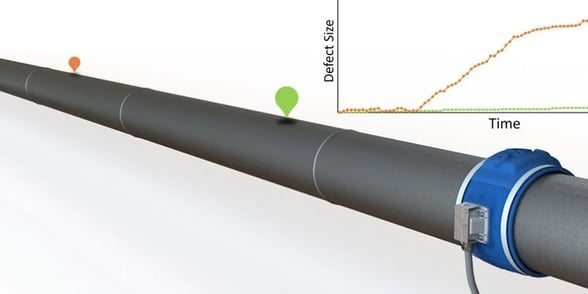
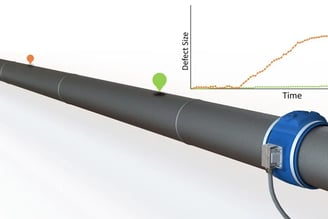
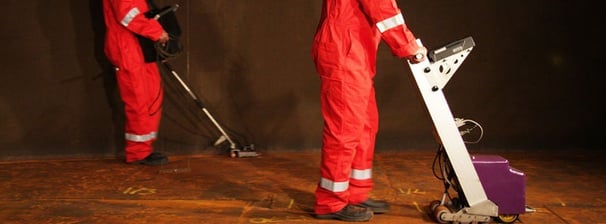
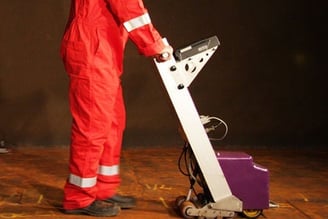
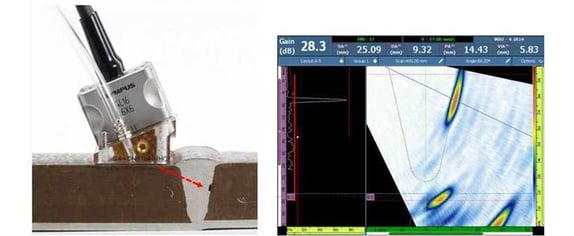
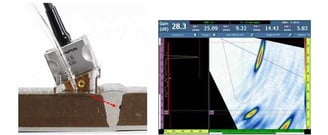
12. Kiểm tra rò rỉ từ thông – Magnetic Flux Leakage (MFL)
Magnetic Flux Leakage (MFL) là một phương pháp kiểm tra không phá hủy sử dụng từ trường mạnh để phát hiện các khuyết tật trong cấu trúc thép. Quá trình này bắt đầu bằng việc tạo ra một từ trường mạnh trên vật liệu cần kiểm tra, thường là thông qua một nam châm. Sau đó, các cảm biến được sử dụng để theo dõi sự thay đổi trong dòng từ trường hoặc mật độ từ trường, điều này có thể chỉ ra các vấn đề như mòn, ăn mòn hoặc rỗ trên bề mặt vật liệu.
Với MFL, kỹ thuật viên có thể đánh giá các vấn đề trên các cấu trúc lớn, như đường ống, tàu, và các công trình thép mà không cần phải làm hỏng hoặc tháo dỡ cấu trúc đó. Phương pháp này rất hiệu quả trong việc kiểm tra các vết nứt bề mặt hoặc khuyết tật khu vực mỏng mà không làm ảnh hưởng đến vật liệu hoặc gây gián đoạn quá trình hoạt động.
Kỹ thuật viên thường phải có kiến thức sâu về khoa học từ trường để áp dụng MFL một cách chính xác và hiệu quả.
11. Kiểm tra rò rỉ bằng khí - Leak Testing
Leak Non-Destructive Testing (NDT) là quá trình kiểm tra các vết rò rỉ trong các bình chứa hoặc cấu trúc để phát hiện các khiếm khuyết mà không làm hỏng vật liệu. Phương pháp này rất quan trọng trong việc duy trì an toàn và hiệu quả hoạt động của các hệ thống công nghiệp, đặc biệt là trong các ngành như dầu khí, hóa chất, và năng lượng.
Có nhiều phương pháp để thực hiện kiểm tra rò rỉ:
Sử dụng đồng hồ đo áp suất: Kiểm tra mức độ giảm áp suất trong hệ thống để xác định liệu có sự rò rỉ hay không.
Kiểm tra bọt xà phòng: Phương pháp đơn giản nhưng hiệu quả, bôi xà phòng lên các điểm nghi ngờ và quan sát sự xuất hiện của bọt khí.
Thiết bị nghe điện tử: Các cảm biến điện tử được sử dụng để phát hiện âm thanh của các khí thoát ra, giúp xác định vị trí và mức độ của rò rỉ.
Leak Testing giúp phát hiện sớm các vấn đề tiềm ẩn, từ đó tiết kiệm chi phí bảo trì và nâng cao độ tin cậy của hệ thống trong môi trường vận hành.
10.Kiểm tra siêu âm mảng pha – Phased Array Ultrasonic Testing (PAUT)
Phased Array Ultrasonic Testing (PAUT) là một phiên bản nâng cao của phương pháp kiểm tra siêu âm truyền thống. PAUT sử dụng một mảng đầu dò với nhiều phần tử siêu âm độc lập, mỗi phần tử có thể phát ra sóng siêu âm độc lập. Điều này cho phép kỹ thuật viên kiểm soát cách thức mỗi phần tử phát ra sóng và có thể điều khiển hướng, tiêu điểm của các chùm sóng siêu âm.
Với khả năng điều chỉnh góc và độ sâu của sóng âm, PAUT dễ dàng tạo ra hình ảnh cắt ngang của vật liệu hoặc thiết bị, giúp phát hiện các khuyết tật ở nhiều tầng và vị trí khác nhau. Điều này đặc biệt hữu ích khi cần kiểm tra các vật liệu dày hoặc cấu trúc phức tạp, nơi các phương pháp kiểm tra siêu âm truyền thống có thể gặp khó khăn.
Một ứng dụng phổ biến của PAUT là sử dụng đầu dò ảo để thu thập dữ liệu, giúp kiểm tra mà không cần tiếp xúc trực tiếp, tiết kiệm thời gian và tăng độ chính xác
9. Kiểm tra sóng dẫn – Guided Wave Testing (GWT)
Guided Wave Testing là phương pháp kiểm tra không phá hủy sử dụng sóng siêu âm lan truyền theo chiều dài của ống để phát hiện khuyết tật. GWT rất hữu ích trong việc kiểm tra đường ống dài, đặc biệt ở những vị trí khó tiếp cận như chôn ngầm, treo cao, hoặc bọc cách nhiệt.
Trong quá trình kiểm tra, sóng siêu âm được truyền dọc theo thành ống và phản xạ trở lại khi gặp các bất thường như ăn mòn, mất vật liệu, hoặc nứt. Dữ liệu thu được sẽ truyền về máy tính để phân tích và xác định chính xác vị trí hư hỏng.
Có hai dạng kiểm tra phổ biến:
GW MRUT (Medium-Range Ultrasonic Testing): phạm vi kiểm tra trung bình.
GW LRUT (Long-Range Ultrasonic Testing): cho phép kiểm tra hàng trăm mét đường ống từ một vị trí duy nhất.
GWT giúp tiết kiệm thời gian, chi phí và giảm thiểu gián đoạn sản xuất – một giải pháp lý tưởng cho ngành dầu khí, hóa chất, năng lượng và nhiều lĩnh vực công nghiệp khác
8. Kiểm tra ống bằng dòng điện xoáy – EC Tube Inspection
EC Tube Inspection là một phương pháp kiểm tra không phá hủy rất quan trọng trong ngành nhiệt điện và trao đổi nhiệt, nơi các ống trao đổi nhiệt cần được kiểm tra định kỳ để đảm bảo hiệu suất và an toàn.
Phương pháp này sử dụng kỹ thuật Eddy Current Testing (ET) để phát hiện các lỗi như mòn thành ống, ăn mòn, nứt theo chu vi và các khuyết tật khác. Việc kiểm tra có thể được thực hiện từ mặt ngoài (OD) trong giai đoạn sản xuất, hoặc từ mặt trong (ID) khi thiết bị đang vận hành.
Thiết bị kiểm tra ống hiện đại có thể sử dụng nhiều kênh và đầu dò khác nhau như ET, MFL (Magnetic Flux Leakage), IRIS (siêu âm phản xạ quay), RFT (Remote Field Testing), NFT (Near Field Testing), và ECA (Eddy Current Array). Các đầu dò này sẽ di chuyển bên trong ống để phát hiện khuyết tật một cách toàn diện và chính xác.
7. Kiểm tra phát xạ âm – Acoustic Emission Testing (AE)
Acoustic Emission Testing là phương pháp NDT dùng để phát hiện khuyết tật thông qua sóng âm phát ra từ bên trong vật liệu khi nó chịu tải trọng hoặc ứng suất. Kỹ thuật viên sử dụng các cảm biến nhạy để ghi lại các xung âm (acoustic bursts) phát ra từ những hiện tượng như nứt gãy, bong tách hay biến dạng.
Hệ thống AE ghi lại vị trí, cường độ và thời gian xuất hiện của các sóng âm, từ đó xác định nơi xảy ra sự cố hoặc vùng có nguy cơ hư hỏng. Phương pháp này đặc biệt hữu ích khi cần giám sát trực tiếp trong quá trình vận hành, ví dụ như kiểm tra bồn áp lực, bình chứa hoặc kết cấu lớn.
AE phù hợp với nhiều ngành công nghiệp như dầu khí, hàng hải, hàng không và xây dựng – nơi cần theo dõi an toàn của hệ thống mà không dừng hoạt động.
6. Kiểm tra dòng điện xoáy (ET – Eddy Current Testing)
Eddy Current Testing là phương pháp kiểm tra không phá hủy dựa trên hiện tượng cảm ứng điện từ. Khi một cuộn dây mang dòng điện xoay chiều được đưa gần một vật dẫn điện, nó sẽ tạo ra các dòng điện xoáy trong vật liệu. Nếu có khuyết tật như vết nứt hoặc ăn mòn, các dòng điện này sẽ bị nhiễu loạn, tạo ra tín hiệu bất thường.
Phương pháp này hoạt động tốt nhất với vật liệu không nhiễm từ (non-ferrous) như nhôm, đồng hoặc thép không gỉ. ET thường được sử dụng để kiểm tra vết nứt bề mặt và gần bề mặt, đặc biệt hiệu quả khi áp dụng cho kim loại, mối hàn và ống trao đổi nhiệt.
ET mang lại độ chính xác cao, tốc độ nhanh và không cần tiếp xúc trực tiếp với vật thể, nhưng chỉ giới hạn ở vật liệu dẫn điện.
1. Kiểm tra bằng mắt thường (VT – Visual Testing)
Visual Testing là phương pháp kiểm tra không phá hủy cơ bản nhất. Kỹ thuật viên quan sát trực tiếp thiết bị, vật liệu hoặc kết cấu để phát hiện các khuyết tật rõ ràng như nứt, ăn mòn, biến dạng. Trong một số trường hợp khó tiếp cận, họ có thể sử dụng thiết bị hỗ trợ như camera nội soi (Remote Visual Inspection – RVI).
Đây là bước kiểm tra đầu tiên rất hiệu quả để đánh giá sơ bộ tình trạng của vật thể. Tuy nhiên, nếu cần phát hiện các lỗi sâu hơn hoặc không nhìn thấy bằng mắt thường, cần kết hợp với các phương pháp NDT nâng cao khác.
2. Kiểm tra từ tính (MT – Magnetic Particle Testing)
Phương pháp này được sử dụng để phát hiện khuyết tật trên bề mặt hoặc gần bề mặt của các vật liệu từ tính như thép hoặc sắt. Kỹ thuật viên tạo ra một từ trường trong vật liệu cần kiểm tra, sau đó rắc các hạt từ (thường là bột sắt) lên bề mặt.
Nếu có khuyết tật như vết nứt, sự gián đoạn trong dòng từ trường sẽ khiến các hạt từ tập trung tại vị trí đó – giúp dễ dàng nhận biết bằng mắt thường hoặc qua ánh sáng huỳnh quang.
Magnetic Particle Testing là phương pháp hiệu quả, nhanh chóng và an toàn, không gây hại cho người kiểm tra hay làm ảnh hưởng đến vật liệu.
5. Chụp bức xạ (RT – Radiographic Testing)
Radiographic Testing là phương pháp kiểm tra không phá hủy sử dụng bức xạ tia X hoặc tia gamma để đánh giá bên trong vật liệu mà không cần cắt phá. Khi kiểm tra vật liệu mỏng, kỹ thuật viên thường dùng tia X; với vật liệu dày hoặc đặc hơn, tia gamma sẽ được sử dụng nhờ khả năng xuyên sâu mạnh hơn.
Tia bức xạ được chiếu qua vật thể và thu lại bằng phim công nghiệp hoặc các thiết bị số như chụp cắt lớp (CT scan), chụp ảnh kỹ thuật số (DR), hay chụp ảnh số hóa (CR). Những vùng có khuyết tật sẽ hiện rõ do mật độ vật chất thay đổi làm giảm hoặc chặn dòng tia.
RT cung cấp hình ảnh trực quan rõ ràng và có thể lưu trữ lại để phân tích sau, nhưng cần tuân thủ nghiêm ngặt các quy định an toàn vì liên quan đến phóng xạ.
4.Kiểm tra siêu âm (UT – Ultrasonic Testing)
Ultrasonic Testing sử dụng sóng siêu âm tần số cao để kiểm tra các đặc tính bên trong của vật liệu mà không gây hư hại. Trong quá trình kiểm tra, sóng âm được truyền vào vật thể cần khảo sát; nếu gặp khuyết tật như vết nứt, rỗng hoặc phân lớp, sóng sẽ phản xạ trở lại tạo thành xung dội (pulse echo).
Kỹ thuật viên dựa vào thời gian và cường độ của tín hiệu phản xạ để xác định vị trí và kích thước của khuyết tật bên trong. UT rất phù hợp cho kiểm tra mối hàn, thép tấm dày và các kết cấu quan trọng đòi hỏi độ chính xác cao.
3. Kiểm tra thẩm thấu chất lỏng (PT – Liquid Penetrant Testing)
Liquid Penetrant Testing là phương pháp dùng để phát hiện các khuyết tật mở ra bề mặt như vết nứt, rỗ hoặc lỗ kim trên vật liệu kim loại và phi kim. Kỹ thuật viên sẽ bôi một loại chất lỏng đặc biệt (có chứa thuốc nhuộm màu hoặc huỳnh quang) lên bề mặt vật cần kiểm tra.
Sau một thời gian thẩm thấu, họ lau sạch phần dung dịch thừa, để lại phần chất lỏng rò rỉ vào các vết nứt. Với dung dịch huỳnh quang, có thể sử dụng đèn UV để dễ dàng phát hiện khuyết tật. Phương pháp này rất nhạy với lỗi bề mặt và có thể dễ dàng làm sạch sau khi kiểm tra.
Bảng so sánh các phương pháp kiểm tra không phá hủy
đóng góp ý kiến
info@nudgeinspect.com
© 2025. NudgeInsepct All rights reserved.